Efficiency During the Drying Process
Low Energy Consumption Through Intelligent Air Circulation.
A constant heat distribution throughout the entire burner assembly is accomplished by the geometry of the burner assembly and the adjustable exhaust flap. Through a large opening in the outer cylinder the constantly distributed heat is evenly spread over the entire load in the inner cylinder.
High air re-circulation for low energy consumption
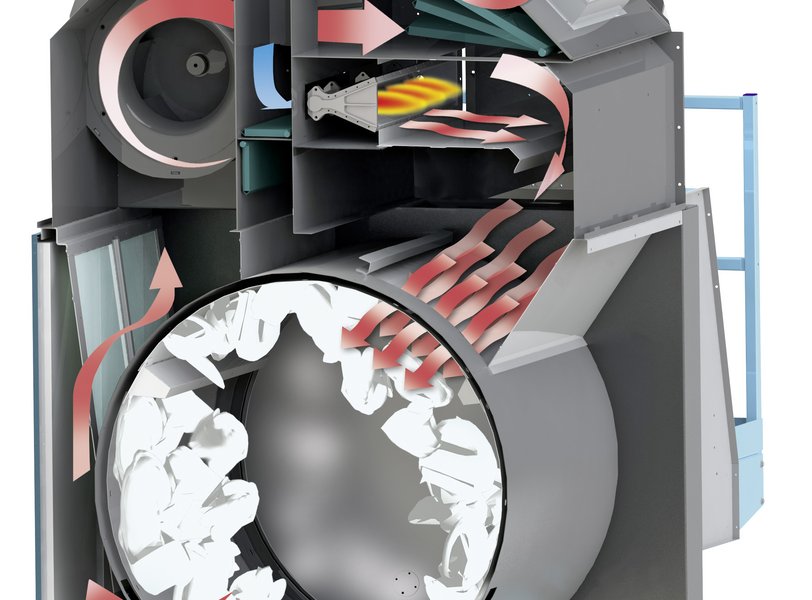
During the continuing drying process, the amount of exhaust and inlet air decreases within the drying process. Depending on the drying level of the goods, the majority of the exhaust air is recirculated by a separate exhaust flap, achieving an optimum amount of air re-circulation. The already heated air stays within the process. The necessary heat demand created by the atmospheric burner is drastically reduced.
INFRATOUCH CONTROLLING
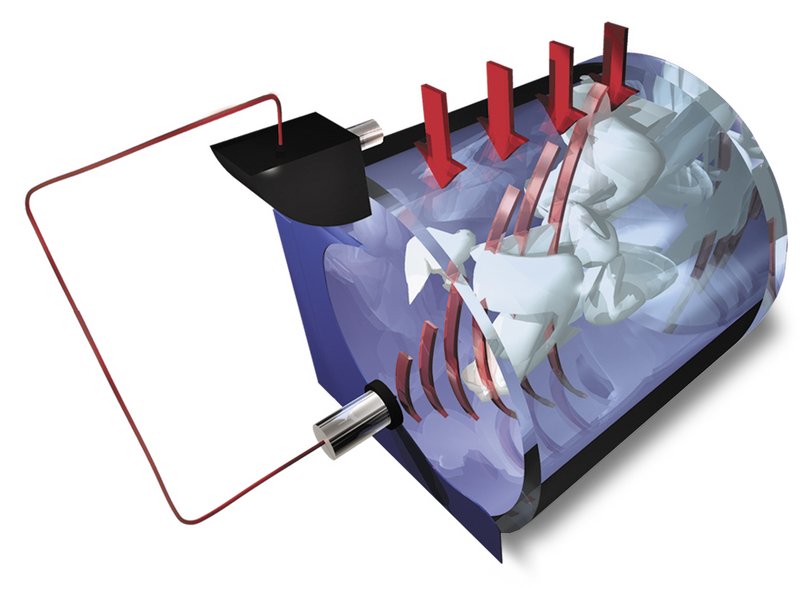
For the exact determination of linen temperature at each point in time utilizing infrared measuring in the inner cylinder. Furthermore the Kannegiesser developed control algorithm allows an accurate drying process.
ECO2Power
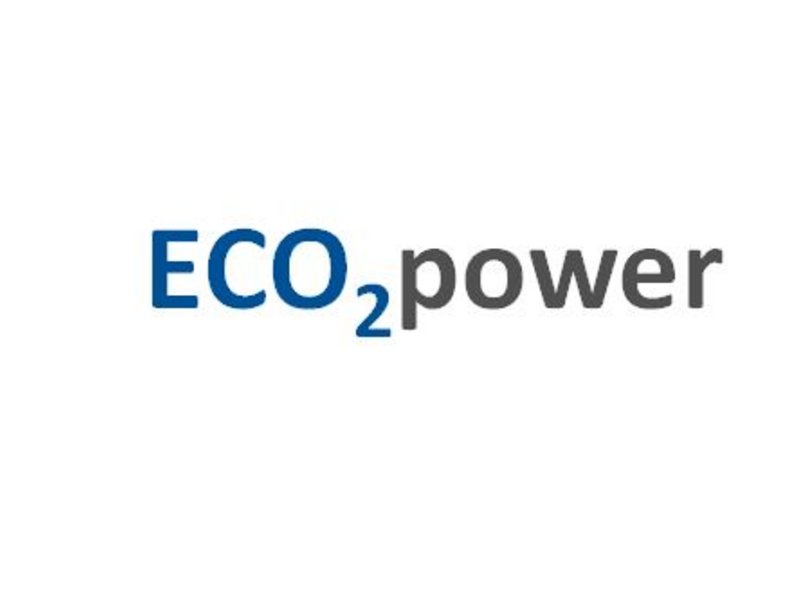
Due to continuously measuring of linen temperature with InfraTouch, together with supply air and exhaust air temperature, the optimal process adjustment will be realized. The result is a maximum air circulation rate and an ideal distribution of the linen in the inner cylinder. The higher the air recirculation in the process, the lower will be the demand for the heat demand supplied by the heating element (gas or steam). The results are not only significant energy savings, but also an exact determination of the material temperature. Both lead to an exact drying process and accurate predetermined drying point.